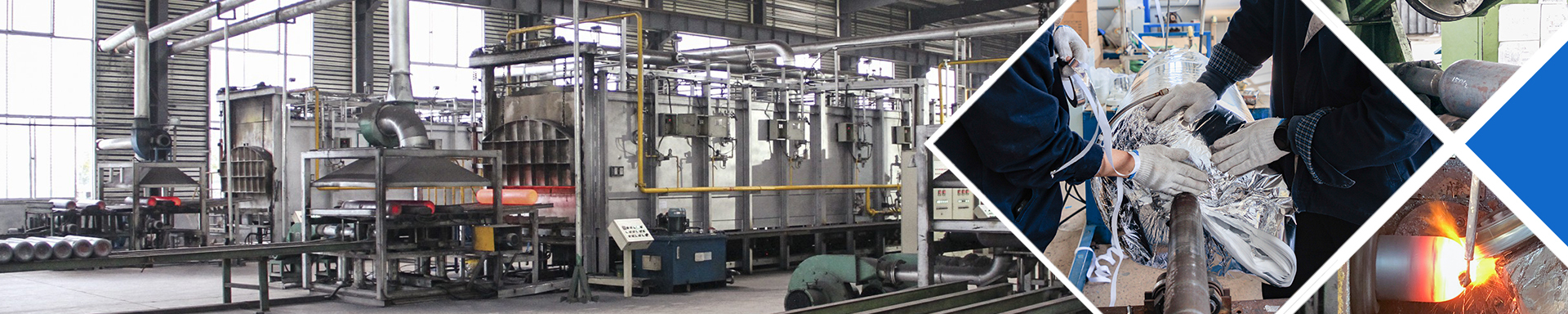
Die Einführung in den Herstellungsprozess nahtloser Zylinder
Seamles-Flaschen sind hochfeste Behälter, die für die Lagerung und den Transport von Druckgasen wie Sauerstoff, Kohlendioxid und Stickstoff verwendet werden. Im Gegensatz zu Schweißzylindern werden nahtlose Zylinder ohne Nähte hergestellt, was sie stärker und langlebiger macht. Sie werden in einer Vielzahl von Branchen eingesetzt, beispielsweise im Gesundheitswesen, in der Automobilindustrie, in der Luft- und Raumfahrt sowie in der industriellen Fertigung.
In der Medizin werden nahtlose Flaschen für die Lagerung und den Transport medizinischer Gase wie Sauerstoff und Stickstoff verwendet, die für den Betrieb von Gesundheitseinrichtungen und Rettungsdiensten von entscheidender Bedeutung sind. In der Automobilindustrie werden nahtlose Zylinder für die Speicherung und Verteilung von komprimiertem Erdgas (CNG) verwendet, das eine sauberere und effizientere Alternative zu Benzin- und Dieselkraftstoffen darstellt.
In der Luft- und Raumfahrt werden nahtlose Zylinder zur Speicherung von Gasen für den Raketenantrieb verwendet. Das hochfeste Material und der überlegene Herstellungsprozess nahtloser Zylinder machen sie ideal für die Anforderungen der Raumfahrt.
In der industriellen Fertigung werden nahtlose Zylinder für die Lagerung und den Transport einer Vielzahl von Gasen verwendet, die beim Schweißen, in der Metallverarbeitung und bei chemischen Prozessen verwendet werden. Sie sind so konzipiert, dass sie Umgebungen mit hohem Druck und extremen Temperaturen standhalten, was sie für den industriellen Betrieb unverzichtbar macht.
Der Produktionsprozess für nahtlose Zylinder umfasst mehrere Schritte der Präzisionstechnik, um einen starken, zuverlässigen Behälter zu schaffen, der komprimierte Gase sicher speichern kann. Im Gegensatz zu Schweißzylindern werden nahtlose Zylinder ohne Nähte oder Verbindungen hergestellt, was sie langlebiger und weniger anfällig für Undichtigkeiten macht.
Der erste Schritt des Prozesses umfasst die Auswahl hochwertiger Materialien wie Stahl oder Aluminium, die dann erhitzt und mithilfe spezieller Maschinen, sogenannter Locher, zu einem Hohlrohr geformt werden. Durch den Durchstechvorgang entsteht ein langes Rohr mit gleichmäßiger Dicke und einheitlichem Durchmesser, das dann auf die entsprechende Länge geschnitten wird.
Der nächste Schritt umfasst den Ziehprozess, bei dem das Rohr durch eine Reihe von Rollen und Dornen geführt wird, um seinen Durchmesser zu verringern und seine Länge zu vergrößern. Durch diesen Prozess entsteht ein nahtloser Zylinder mit einer glatteren und gleichmäßigeren Oberfläche.
Sobald der Ziehvorgang abgeschlossen ist, wird der Zylinder einer Wärmebehandlung unterzogen, um seine Festigkeit und Haltbarkeit zu verbessern. Anschließend wird der Zylinder mithilfe verschiedener zerstörungsfreier Prüftechniken gründlich gereinigt und inspiziert, um etwaige Mängel oder Anomalien zu erkennen, die seine Leistung beeinträchtigen könnten.
Abschließend wird der Zylinder mit einer Schutzschicht überzogen, um Korrosion und Beschädigungen der Oberfläche zu verhindern. Der Beschichtungsprozess umfasst die Oberflächenvorbereitung, das Auftragen einer Grundierung und die Endbearbeitung mit einer haltbaren Farbe.